3DCS Variation Analyst
3DCS is a World Class 3D Tolerance Simulation Tool that allows you to model the effect of variation on an assembly, Determine the "Robustness" of your design, and test Alternative Tolerancing Schemes. 3DCS is a True 3D Tolerance Modeling system that visually depicts variation in your design, and statistically simulate production of your "Virtual Assemblies."
Modeling Variation Graphically
3DCS employs a 3D display similar to high-end CAD systems, allowing users to pan, zoom, and manipulate 3D parts and assemblies. Parts can be imported as IGES data or created directly in the software.
Easy to Use Menus
Designed for Windows, 3DCS features a simple interface with clear menus and toolbars, enabling quick model generation. Engineers familiar with CAD can start modeling in 3-4 days.
Visualize Variation in Real Time
3DCS graphically simulates variation, showcasing features varying with GD&T callouts, parts moving in assemblies, and measurements changing dynamically.
Complete Statistical Data
Uses Monte Carlo simulation to assign tolerance values with distribution options like Normal and Weibull. Outputs include standard deviation, Cp, Cpk, and histograms for visual analysis.
Complete Assembly Diagrams
Provides detailed assembly trees showing relationships, sequences, and associated moves, measures, and tolerances for quick model assessment.
Key Contributors to Variation
Identifies root causes of variation in assemblies, enabling Pareto and sensitivity analysis. Early detection helps refine designs before production investments.
Graphic Tolerance Simulation Software Solutions for CATIA V5
Visually Observe Dimensional Variation
Predicting dimensional variations due to part tolerances as well as assembly process sequences are significant early in the design process before investing into tooling, prototyping and production fixtures and inspection gages. 3DCS provides the power to define, test and modify product and process requirements in a digital environment and the ability to share reliable variation analysis results with the entire product development team. Utilizing 3DCS will enhance existing manufactured products and enable the cost-effective development of exciting new fast-to-market products.
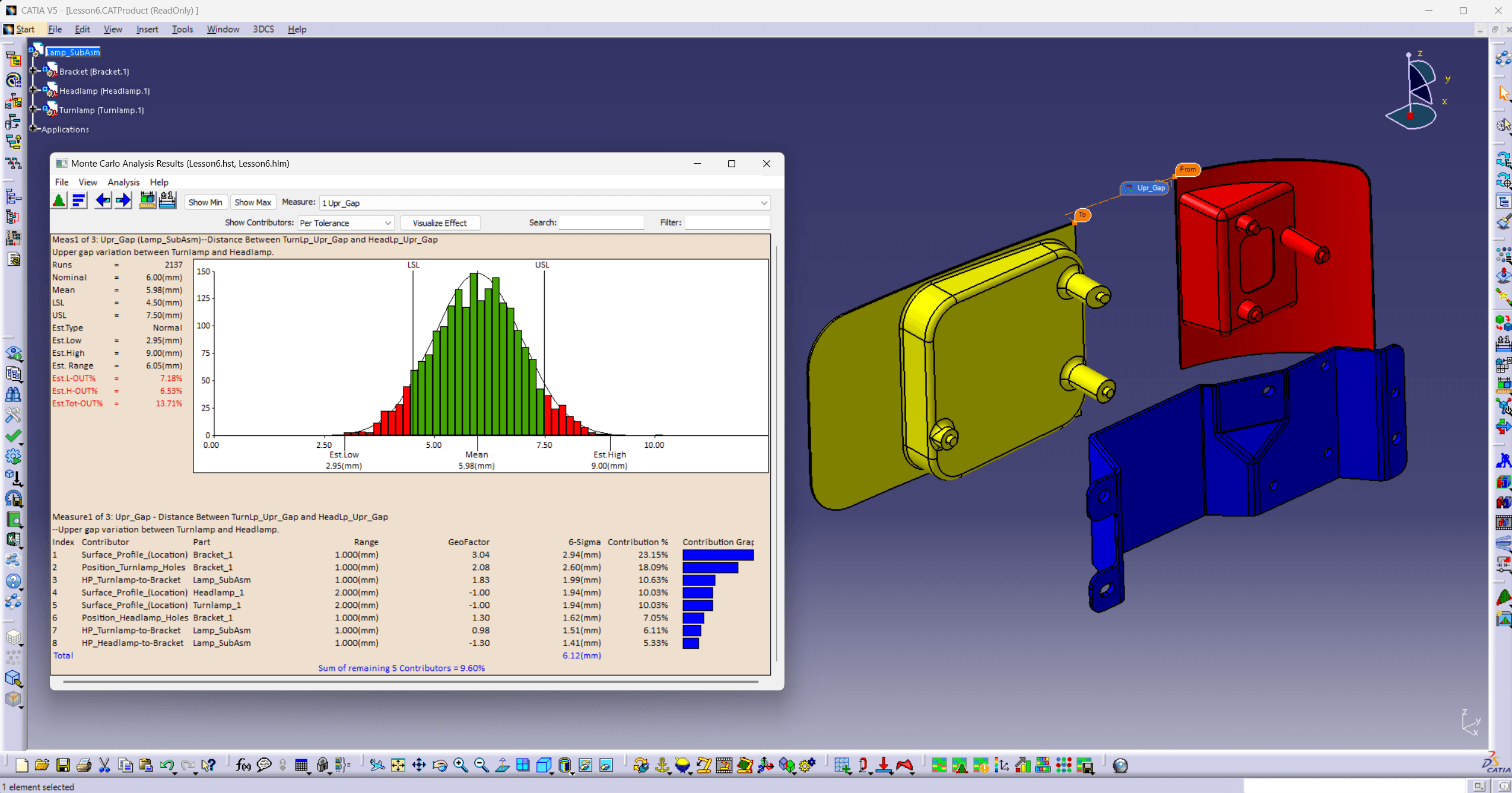
Modeling Variation Graphically
3DCS Designer, CAA V5 Based Graphic Tolerance Simulation Software embedded within CATIA V5. A completely feature-based versatile solution focused specifically on the needs of designers and engineers. 3DCS Designer is a powerful dimensional analysis tool that predicts the amount of part and process variation and highlights their causes. 3DCS Designer quickly evaluates part GD&T early in the product development stage so that desired fit and function (gaps, flush, overall dimensions) specifications are achieved in production.
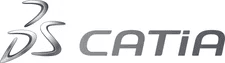
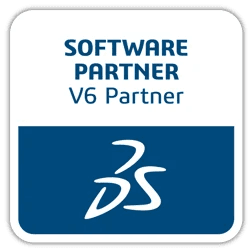
3DCS Analyst, CAA V5 Based
Graphic Tolerance Simulation Software embedded within CATIA V5. With all the same feature-based routines of 3DCS Designer, plus a comprehensive set of point-based routines that provide greater flexibility and a higher degree of accuracy, 3DCS Analyst is the ideal tool for complex tolerance simulation modeling of part and process variation in multi-stage assemblies. 3DCS Analyst allows manufacturers to prevent build problems by quickly evaluating assembly GD&T, tooling and sequencing ahead of time.
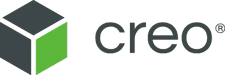
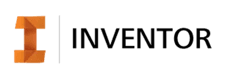
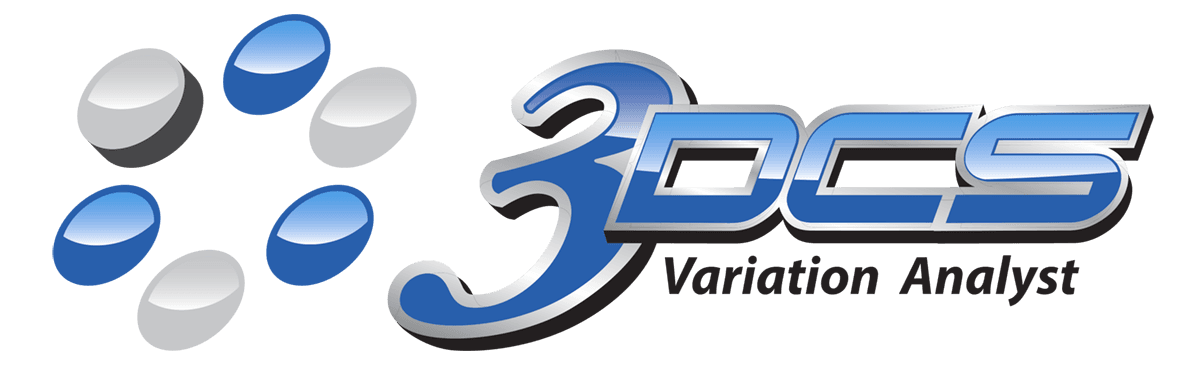
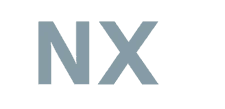
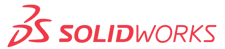
Business Values
Optimize Product Designs and Processes
3DCS, CAA V5 Based allows CATIA users to evaluate design and assembly concepts up front, where problem areas can be identified early in the product development cycle. Optimizing for dimensional integrity improves the robustness of design and processes by maximizing part tolerances while controlling the dimensional assembly requirements of the final assembly.
Reduce Cycle Time & Rework Costs
Shorten development time, accelerate time to market and reduce costs by utilizing the capability of 3DCS, CAA V5 Based for digital prototyping. By maximizing part tolerances while still controlling dimensional assembly requirements, manufacturing costs can be reduced with less rework to tools and gages, minimized scrap and reduced number of warranty defects. 3DCS, CAA V5 Based reduces your bottom line and significantly improves product quality by validating that parts fit and function together before production starts.
Target Users
- 3DCS, Designer, CAA V5 Based:
A core solution to meet the day-to-day demands of designers and engineers - 3DCS, Analyst, CAA V5 Based:
A comprehensive tool for specialists who need to perform complex iterative analysis
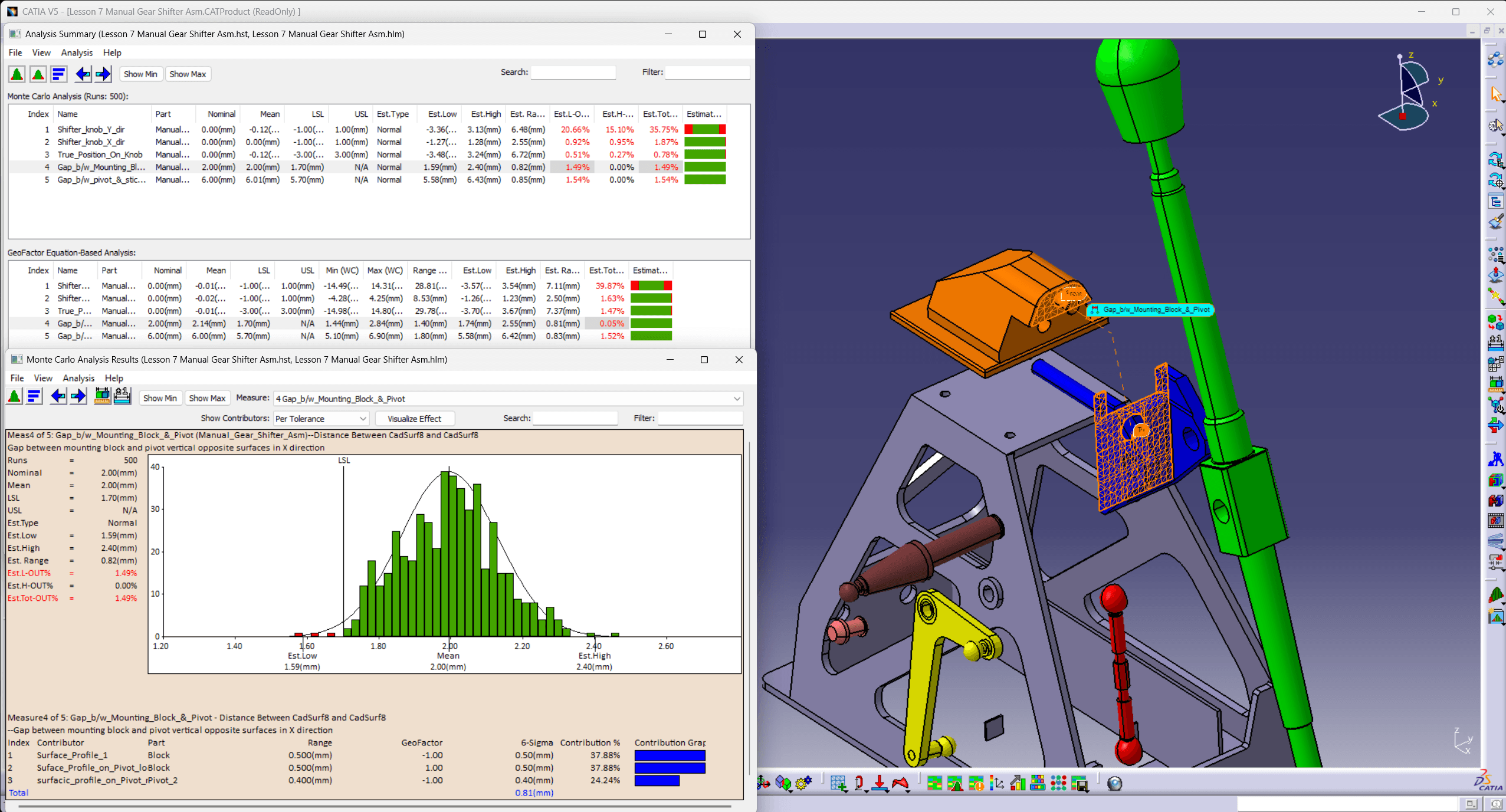
Key Product Features
- •Identify Contributors - Localize tolerances and assembly processes responsible for variation
- •Incorporate embedded CATIA V5 FTA or CATIA V4 FD&T and visually display part variation
- •Work Seamlessly with existing CATIA V4 data
- •Animate Build Sequences - Create exploded views and display parts moving sequentially to their final assembled positions
- •Animate Variation On-Screen - Users can visualize clearances & interferences, sweep parts and assemblies within their statistical extremes
- •Quickly Build Analysis Models with an easy-to-use and easy-to-learn graphical user interface, all within a single CATIA V5 window
- •Create Models Without Geometry - Perform tolerance analysis with 3DCS, Analyst, CAA V5 Based before CAD geometry exists
- •Specify Distribution Types - Select from a comprehensive set of statistical distributions with 3DCS, Analyst, CAA V5 Based to represent differing manufacturing processes
- •Supports both Windows and UNIX Operating Systems
- •Three Types of Analysis Outputs - Monte Carlo Simulation, High-Low-Mean (Sensitivity Analysis) and GeoFactor Analysis
- •Perform What-If Analysis - Learn the impact on the final assemblies before costly design changes need to be made
- •Evaluate Geometric Factors in critical dimensions of parts and assemblies and enhance the robustness of their designs
- •Reuse Models - Capture commonly used processes and build your own library of easily accessible models
- •Update Models Automatically - Direct links to design geometry result in quick and efficient tolerance model updates
- •Enhance Dimensional Integrity with greater product quality and improve Product Lifecycle Management
- •Use Manufacturing Data - Import real world data into 3DCS, Analyst, CAA V5 Based for root cause analysis to improve existing build processes
- •Communicate Results quickly and simultaneously to the entire product development team
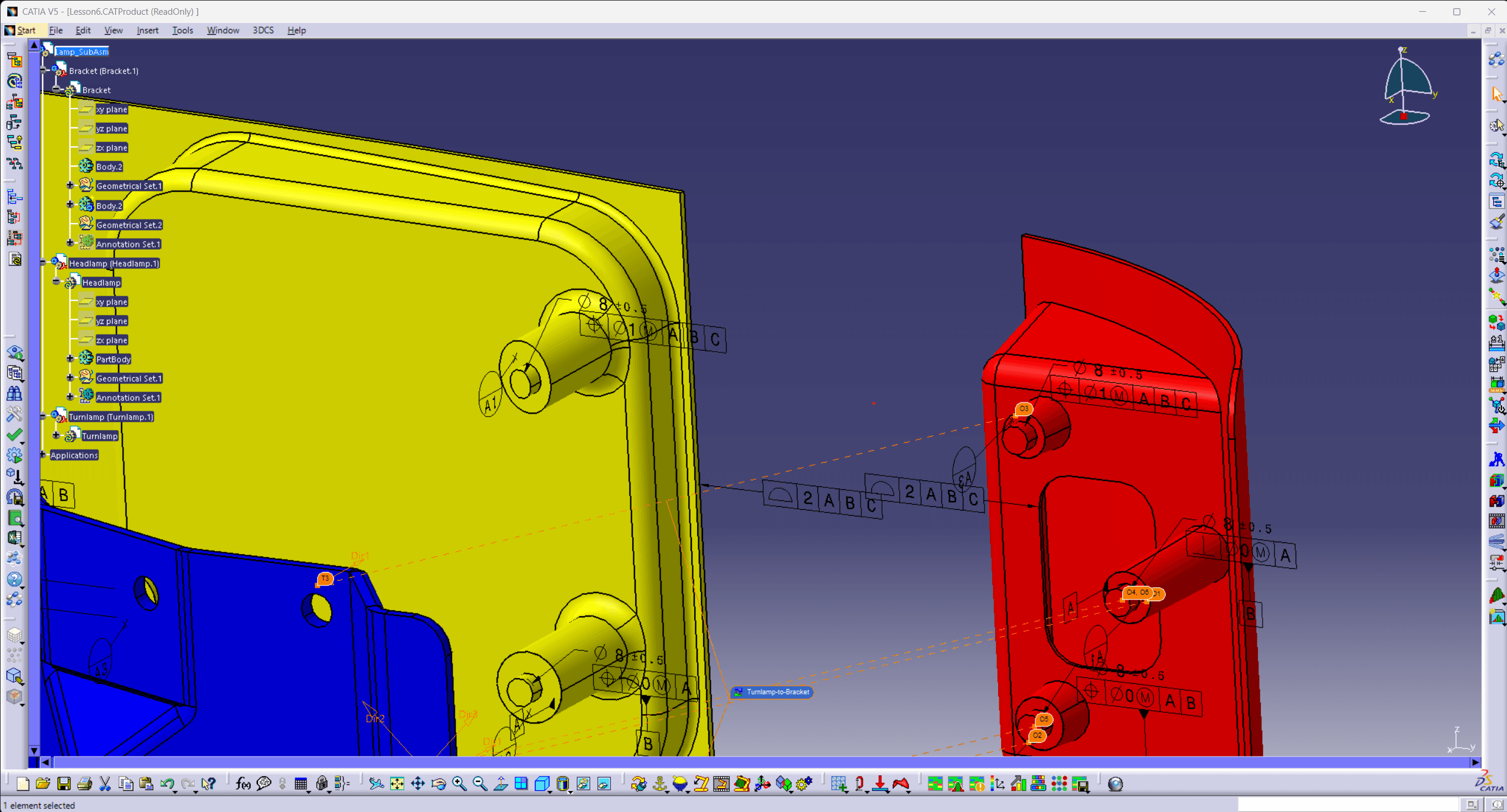